machinist@lists.ibiblio.org
Subject: Machinist
List archive
- From: Lawrence London <lfljvenaura@gmail.com>
- To: machinist@lists.ibiblio.org
- Subject: [machinist] Wringing Gage Blocks
- Date: Thu, 27 Jul 2017 18:46:48 -0400
Wringing Gage Blocks
http://starrett-webber.com/GB46.html
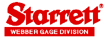
BACK to USE and CARE
GAGE BLOCK HEADER PAGE
Wringing Gage Blocks
Wringability is an important property of gage blocks. In fact, gage block specifications recommend replacing blocks that have lost their ability to wring. Not everyone uses gage blocks in wrung combinations, but wringability is a test on the integrity of the surface condition of the gage block. Gage blocks that don’t wring may give erratic and unreliable results. The fact that gage blocks wring is incorporated into the lengths of the blocks themselves. Gage block length is defined as an interferometric measurement when the gage block is wrung to a flat platen. This includes one wringing film in the defined length of the gage block.
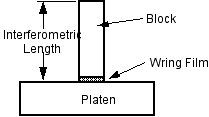
This definition is very useful. When gage blocks are assembled in combinations, no additional correction factor for wringing films needs to be added to the length of the combination.
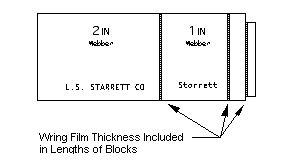
Wringability itself may be defined as the ability of two surfaces to adhere tightly to each other in the absence of external means. (They are not magnetized or clamped together.) Wringing requires two smooth, flat surfaces with surface finishes of 1 microinch AA or better. For gage blocks, it becomes difficult to wring surfaces if the flatness starts to exceed 5 microinches. The sources of the forces holding gage blocks together are thought to come from: 1. Air pressure from the surrounding environment as the air is squeezed out when the blocks are slid together. 2. Surface tension from oil that remains on the gage blocks or water vapor from the air acts as a glue to hold them together. 3. When two very flat surfaces are brought into such close contact with each other, this allows an interchange of electrons between the atoms of the separate blocks, which creates an attractive molecular force. (This force will remain even in a vacuum or if no oil or water is present on the blocks.) The last two sources are thought to be the most significant. Preparation of Gage Blocks Prior to Wringing Make sure that the blocks to be wrung are free from nicks and burrs. It is important that all nicks and burrs be removed BEFORE attempting to wring blocks together because a burr on one block may damage the surface of the other block. Blocks may be checked for burrs with a gage block stone before wringing. A gage block stone with serrated grooves is recommended because it gives a better "feel" for nicks and burrs that catch the edges of the serrations. Badly nicked surfaces will click as a nick passes along the serrations.
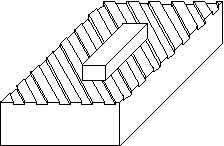
Wringing Gage Blocks 1. Make sure that blocks are clean. 2. Wipe the surfaces of the blocks to be wrung gently across the oiled Wring Pad. (See figures below.) 3. Wipe these surfaces on the dry pad, removing as much oil as possible. 4. Slide the surfaces of the blocks together as shown. Apply pressure while sliding the blocks. The blocks should slide together without any feel of bumps or scratching, and should adhere to each other strongly after being rotated into place.
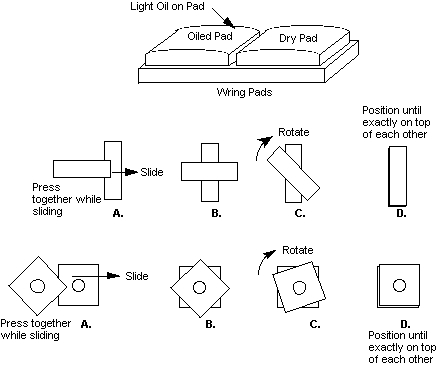
Wringability is an important property of gage blocks, and is fortunately a quality that can be controlled and monitored readily by the user of the blocks. With proper use and care, gage blocks will provide long, reliable, accurate service.
BACK to USE and CARE
GAGE BLOCK HEADER PAGE
GB46
- [machinist] Wringing Gage Blocks, Lawrence London, 07/27/2017
Archive powered by MHonArc 2.6.24.